Dernière mise à jour le 24 mai 2022
Le principe du juste à temps (JAT), aussi appelé flux tendus, consiste à produire strictement la quantité nécessaire afin de répondre immédiatement aux besoins du client. Cette méthode présente des avantages : baisse des délais, augmentation de la qualité, diminution des temps morts et donc des coûts de production…Il permet à l’entreprise de fonctionner sans stock, à l’exception des en-cours de fabrication et du transport.
Plusieurs degrés de juste à temps
Il existe plusieurs degrés de juste à temps :
- L’entreprise n’a pas de stock de produits finis. Ainsi, dès que les produits finis sont fabriqués, ils sont expédiés aux clients ;
- L’entreprise n’a pas de stock de produits semi-finis. Ainsi, dès que les produits semi-finis sont fabriqués, la fabrication des produits finis est lancée ;
- L’entreprise n’a pas de stock de matières premières. Ainsi, dès que la matière première est réceptionnée, la fabrication est lancée.
Les avantages du système
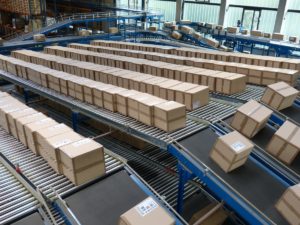
S’il est correctement géré, il y a de nombreux avantages dans ce système :
- Baisse des délais ;
- Augmentation de la qualité ;
- Baisse des coûts de production : moins de manutention, de temps mort, de défaut, de pannes ;
- Baisse des coûts de stockage : baisse de la surface et donc du coût d’entreposage ainsi que des charges afférentes, baisse des charges de personnel assurant le stockage, baisse des frais financiers (coût du financement du stockage qu’il soit interne ou externe) et amélioration du BFR ;
- Simplification des méthodes comptables: l’inventaire annuel est plus simple avec un nombre inférieur d’articles à compter et la dépréciation des stocks est moindre en raison de l’obsolescence quasi inexistante. A noter également que le système du juste à temps va souvent de paire avec un système d’échange de données informatisées (EDI). Cela permet d’automatiser les flux commandes – lancement de la production – expédition – livraison – facturation – enregistrement comptable.
Mettre en place un système de juste à temps
Mettre en place un système JAT passe par une plus grande réactivité et flexibilité dans la production :
- Flexibilité quantitative : surdimensionnement de la capacité de production pour faire face à la demande ;
- Flexibilité qualitative : changement rapide de fabrication ;
- Rationalisation des produits : produits plus simples, demandant moins d’intervention ;
- Mise en ligne des machines : organisation du processus en ligne ;
- Amélioration de la fiabilité des équipements : maintenance préventive :
- Relation clients fournisseurs plus étroite et mise en place de l’EDI ;
- Planification de la production et des approvisionnements ;
- Méthode SMED (Single Minute Exchange of Die) ou en français échange d’outil en moins de dix minutes. En effet, la production peut être immobilisée un certain temps entre la fabrication de la dernière pièce d’une série et de la première pièce de la série suivante. Ce temps se décompose entre préparation des outils, de la machine, l’échange d’outils, la mise en place et le réglage des outils et les essais jusqu’à l’obtention d’une première bonne pièce ;
- Chasse aux gaspillages avec les 7 mudas : surstock, surproduction, mouvements inutiles, temps d’attente, rebuts-retouches, corrections, transport ;
- Elimination des causes des petits problèmes avec les 5 S: trier, ranger, nettoyer, standardiser et respecter ;
- Méthode kanban qui consiste à utiliser des étiquettes pour matérialiser les commandes.
Pour en savoir plus, consultez notre article : les outils du lean management
Merci pour ces détails sur le juste a temps qui n’est pas forcément la méthode la plus connue en logistique.